Why Join the Digital Dance? Dancing with the Stars[1], or in the UK Strictly Come Dancing as the original is named, pairs celebrities with
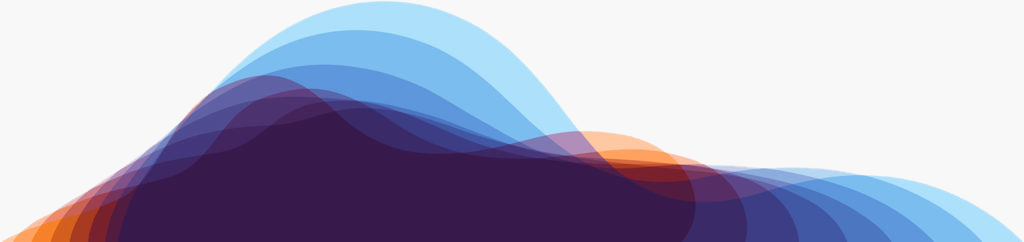
The blog for passionate planners
Tips, stories, and insights to better manage work, improve productivity and enhance collaboration.
The 2017 State of Manufacturing Technology says that“90% of respondents are using cloud-based productivity applications, double the number in 2016.”
If you’re a project manager with big data skills and knowledge, the manufacturing industry wants to talk to you.
If your weekend plans look anything like mine, you’ll be reading. A lot. My favorite thing to do on a warm Saturday afternoon is
Once the stuff of science fiction, the idea of artificial intelligence (AI) carrying out tasks that only humans could previously achieve has become a
In a fiercely competitive global market, manufacturers’ product margins face increasing pressure, forcing them to look for ways to differentiate their businesses. Many are