Anyone who has ever led a manufacturing project can attest to the fact that they have unique challenges. Nearly all projects iterate through some version of the “planning, execution and control” cycle, but manufacturing takes that to new levels. This is particularly true when you are going to be churning out a high volume of the same thing, such as an automobile part or an electrical component.
Watching the end result of a project manifest itself as thousands (or millions) of an item rolling off of a conveyer belt can elicit an almost Zen-like pleasure. But it also can be accompanied by a sinister side effect: variance. Variance is the enemy of production, but the trouble is that virtually everything varies somewhat in this universe if you measure it carefully enough. There are simply tiny fluctuations present in everything we see and touch. This includes even the most precise goods made today. Addressing variance is where the processes of Six Sigma shines.
What’s a “Sigma”?
Six Sigma is a group of processes that were born at Motorola and made famous at General Electric. Now it is used in many of the best manufacturing companies around the world. Before we get into the specifics of what Six Sigma is and why it’s important, let’s discuss what a sigma is and why it matters.
When you are manufacturing a product, standardization matters. In fact, whether or not the product is a “quality” product depends upon the product falling within a certain range of specifications.
As stated earlier, everything deviates from a standard if you measure it carefully enough. The goal is to take measurements that are fine enough to capture these fluctuations. You average these measures together to determine the mean, and then you can calculate the standard deviation of all of those numbers. This simply tells how diverse your data set is. Diversity can be a good thing but not when you are dealing with products that are supposed to be standardized!
Ideally, your measurements should be grouped very closely to the mean. This would indicate a low standard deviation, which is desirable. On the other hand, a high standard deviation indicates a lot of variances, which means your processes are probably not under control.
This is where we get the word “sigma.” A sigma, abbreviated as “σ“, represents a distance on either side of the mean. A single standard deviation from the mean is called “one sigma.” So one sigma quality means that only the items with measurements that fell within one standard deviation passed quality inspection. Unfortunately, this only equates to about 31 percent. Three sigma quality is much better since it means that many more passed through quality. That gets us up to over 93 percent quality.
If you have achieved six sigma quality, you have only 3.4 defects for every one million products that your organization produces. This is considered to be world class.
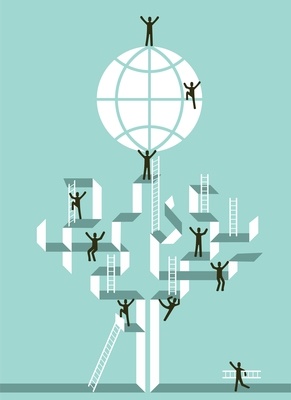
What Six Sigma Looks Like in the Real World
One way it has been described is that one sigma quality equates to an error per page in a book. Three sigma quality equates to a single error in the whole book. Six Sigma quality would have only a single error in the entire library. When you achieve the level of six sigmas, you have essentially removed most of the things that can be controlled. Remaining defects will fluctuations in line with the nature of materials, etc.
The 5 Steps of Six Sigma
But the goal is not simply to achieve this quality. The goal is to be able to achieve it repeatedly and predictably every time you manufacture the product. This generally involves not only the organization performing the project but also the entire supply chain. So Six Sigma has a series of steps to help you achieve world-class quality and sustain it. This family of steps is abbreviated as DMAIC. If you work around Six Sigma, you will see DMAIC a lot. It is an acronym that stands for:
(D)efine
(M)easure
(A)nalyze
(I)mprove
(C)ontrol
Here’s a look at each step:
- Data: The steps that make up DMAIC are based on hard numerical analysis and not simply observation. The team gathers data and those data are used to understand and make decisions. As W. Edwards Deming famously stated, “Without data you’re just another person with an opinion.”This data-driven approach begins with the step of Define. In other words, define the problem, define the scope, and define what success would look like. Steven Covey urged us to “Begin with end in mind”, and this is simply an empirical understanding of what that end should look like.
- Measure is where you take very specific measurements of your current reality. This starts with the output but may grow to include measurements about how the output is being produced.
- Analyze is about coming up with a plan to move from the current measured state to the desired state. It commonly involves root cause analysis so that you are not simply dealing with surface issues.
- The step of Improve takes action to move the current state to the desired state. The previous steps of Define and Analyze are to gain an understanding of what is wrong and how to fix it, but this step takes real steps to bring the product into quality tolerances.
- Control is about making your change consistently repeatable. This is not about a one-time fix. It is about putting the right change policies, and processes in place to produce consistently better products. This can be the most frustrating step in the entire process.
Prevention Over Inspection
A common reaction when looking at this list is: “What happened to inspection?” In other words, how can you have high quality if product inspection is not an integral part? The answer is that Six Sigma, like most modern quality programs values prevention over inspection. It is based on the principle that quality cannot be inspected into a product after it has already been manufactured. Instead, quality is all about prevention. When it comes to delivering quality products, planning always wins over inspection.
The art is to learn to identify, measure, and ultimately eliminate variances. And this is not a one-time activity. It has to be done throughout the project and into subsequent operations because waste is like weeds in a lawn or garden. You get rid of the undesirables but then they inevitably and relentlessly come creeping back in.
Is Six Sigma Right for Your Project?
You can best answer this question by looking at the type of manufacturing or service delivery involved in your project. In cases where the manufacturing is not highly consistent, it may be best to try a different approach. A great example of a Six Sigma project includes Motorola manufactured circuit boards and silicon processors and chips. This was highly repetitive and did not vary much within a product line. On the other hand, consider an aircraft manufacturer that delivers a relatively small quantity of planes that are each configured differently—not a great candidate for Six Sigma?
Taking the steps to achieve world-class quality can be intimidating, but it brings big rewards. If you are ready to learn more about Six Sigma and what it can do for you, the American Society for Quality could be a great place for you to begin.
Did you know that only 2.5% of companies successfully complete 100% of their projects? That’s sign of a bad project management process. How would you rate yours? Take our Project Management Health Check, a 9-question multiple-choice assessment of your project management process.